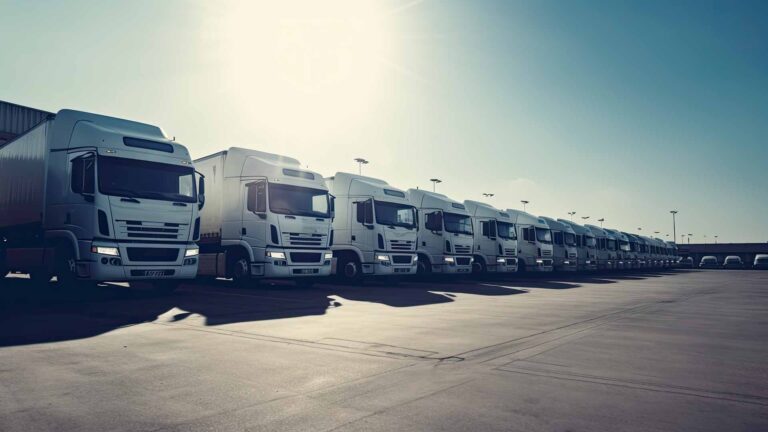
Basic Guide to 3PL (Third Party Logistics)
3PLs provide flexible and scalable logistics solutions can grow with your business. But what is a 3PL and how do they work?
Navigating the world of logistics can be complex and confusing, especially when deciding between third-party logistics (3PL) and fourth-party logistics (4PL) providers. This article will shed light on the differences between these two types of providers, their advantages and disadvantages, and how to determine which is best suited for your business needs.
Third-party logistics, or 3PL, refers to companies that provide logistics services to businesses that need help managing their supply chains. These services can include transportation, warehousing, distribution, and other logistics-related tasks.
3PL providers essentially act as intermediaries between manufacturers, retailers, and consumers, helping to ensure that products are moved efficiently from one point to another.
Fourth-party logistics, or 4PL, is a step beyond 3PL in terms of logistics management. 4PL providers are responsible for overseeing and optimizing the entire supply chain for a client. Unlike 3PL providers, 4PLs don’t own any assets such as trucks, warehouses, or distribution centers. Instead, they leverage their expertise and strategic partnerships to manage the supply chain effectively, often coordinating multiple 3PLs and other service providers to ensure optimal efficiency.
When it comes to logistics providers, businesses have the choice between 3PL and 4PL providers. While both play a role in the logistics process, there are key differences between the two.
While both 3PL and 4PL providers are involved in the logistics process, their focus is different. 3PL providers concentrate on the execution of specific logistics tasks, such as transportation and warehousing. In contrast, 4PL providers focus on the overall management and optimization of the entire supply chain. This distinction means that 4PL providers are concerned with the broader picture of how all logistics processes interact, identifying areas where improvements can be made across the entire supply chain, whereas 3PL providers are more task-oriented and concentrate on individual processes.
3PL providers often own and operate assets like trucks, warehouses, and distribution centers. On the other hand, 4PL providers don't own any assets and instead work with various partners to manage and optimize the supply chain. This difference in asset ownership can impact a company's decision when choosing a logistics provider. Companies that prefer to outsource the ownership and management of assets may find 3PL providers to be a better fit, while those looking for a more strategic approach without the burden of asset ownership may prefer a 4PL provider.
3PL providers typically have a more transactional relationship with their clients, focusing on the delivery of specific services. 4PL providers, however, work closely with their clients as strategic partners, collaborating to optimize the entire supply chain. This means that 4PL providers are more invested in their client's long-term success and growth, as they continuously work together to find and implement supply chain improvements. In contrast, the relationship with a 3PL provider may be more short-term and focused on specific logistics tasks.
3PL providers are primarily responsible for the physical movement of goods, including order fulfillment and delivery. 4PL providers, while not directly handling order fulfillment, oversee and coordinate the entire process to ensure efficiency and cost-effectiveness. This difference in responsibilities means that 4PL providers take a more holistic approach to order fulfillment, managing and coordinating multiple 3PL providers and other service providers, such as carriers and warehouse operators, to ensure seamless integration of all supply chain activities.
3PL providers may offer some level of supply chain optimization, but this is generally limited to their specific service offerings. 4PL providers are dedicated to optimizing the entire supply chain for their clients, leveraging data, technology, and strategic partnerships to identify and implement improvements. This focus on optimization means that 4PL providers can often deliver greater value by identifying and addressing inefficiencies throughout the entire supply chain, rather than just within individual logistics processes.
3PL providers typically communicate directly with customers regarding order status, delivery times, and other logistics-related issues. 4PL providers, however, may take a more hands-off approach, allowing their strategic partners (such as 3PLs) to handle customer communications. This difference can impact the level of control a company has over its customer interactions and may be an important consideration when choosing between a 3PL or 4PL provider.
Both 3PL and 4PL providers can offer cost savings to businesses by streamlining logistics processes. However, 4PL providers often have the potential to deliver more significant cost savings by optimizing the entire supply chain, rather than just individual aspects. These savings can be realized through various means, such as improved efficiency, reduced waste, better utilization of resources, and enhanced coordination between different partners within the supply chain.
When it comes to logistics providers, businesses need to consider the advantages and disadvantages of both 3PL and 4PL providers. By understanding the benefits and drawbacks of both logistics models, businesses can make informed decisions about which type of provider is the best fit for their needs.
Third-party logistics for field services and retail: 3PL providers are commonly used in field services and retail industries, where the focus is on the efficient transportation, warehousing, and distribution of goods. Businesses in these industries often need a wide range of logistics services, making 3PL providers a suitable choice for handling these tasks.
Fourth-party logistics for field service and retail/eCommerce: 4PL providers can also be a valuable asset for field service and retail/eCommerce industries, particularly for businesses looking to optimize their entire supply chain. By offering comprehensive supply chain management, 4PL providers can help these businesses identify areas for improvement and implement strategic changes to drive efficiency and cost savings.
When deciding between 4PL vs. 3PL logistics model for your business, there are several factors to consider:
The choice between 3PL and 4PL providers depends on your business’s specific needs and priorities. By carefully evaluating your requirements and considering the 3PL vs 4PL differences, you can make an informed decision that will help streamline your logistics processes, improve efficiency, and drive cost savings.
Choosing a 3PL provider offers numerous benefits for businesses looking to optimize their logistics operations. By outsourcing logistics functions to a 3PL, companies can save time and money, leverage industry expertise, expand their business reach, and focus on their core competencies. Additionally, 3PLs provide flexibility and scalability, ensuring that logistics solutions can grow with the business. With the right 3PL partner, businesses can effectively manage their supply chain, mitigate risks, and ultimately enhance customer satisfaction.
Need help figuring out the total volume of usable space in your warehouse? We built a simple tool to help you calculate that.
The pallet storage capacity calculator quickly determines the total number of pallets your warehouse can store based on rack configuration.
3PLs provide flexible and scalable logistics solutions can grow with your business. But what is a 3PL and how do they work?
This warehouse management article helps you understand practical advice for any business that is involved in running warehousing operations.
What is a fulfillment center and how does it differ from a distribution center? How do I decide which is right for my business?
There was a time when businesses revolved centrally around the customer and their needs. Decisions were made based on what is best for the customer first. People did what they said they would, and jobs were completed on time. AMS carries on the tradition of customer service today.
AMS is a customer service-centric warehousing and fulfillment company. We have the software, but we don’t replace PEOPLE and SERVICE with software. Being that we are a contract manufacturer as well, we have a lot of expertise and capability that you can rely on and trust.